Newsblog
Bleiben Sie immer auf dem neuesten Stand mit unserem Blog RSS-Feed
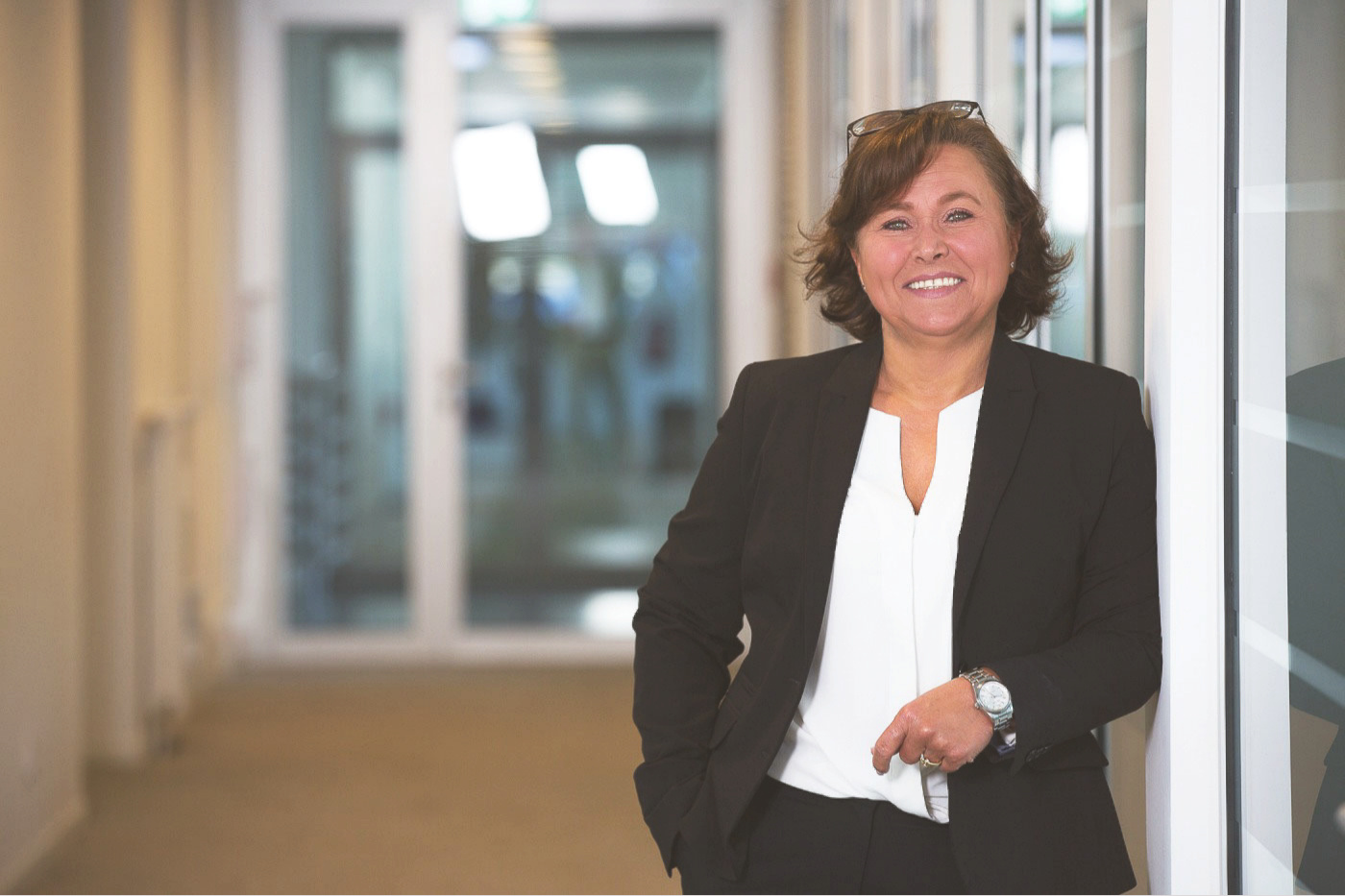
Ihre Ansprechpartnerin im Bereich Marketing
Sprechen Sie mich direkt an oder senden Sie mir eine Bitte um Rückmeldung
Yvonne Faber
Leiterin Marketing
Bleiben Sie immer auf dem neuesten Stand mit unserem Blog RSS-Feed
Sprechen Sie mich direkt an oder senden Sie mir eine Bitte um Rückmeldung
Yvonne Faber
Leiterin Marketing